by Dr Nick McCarthy and Keith Budden, Cenex
Asset and fuel choice for farm vehicles
It is essential to consider vehicle or infrastructure asset replacement cycles. Given that many farm vehicles have working lives of 15 to 20 years, capital investment decisions in the next decade will have limited opportunities for revision before 2050. Although the business case for gas fuels may seem straightforward to the end-user, fuel suppliers need to justify the capital investment over an extended period. Moving away from CO2e emitting fuels on farms is reliant on investment cycles and access to low carbon power trains.
Fuel technologies – and their impact upon vehicle design and powertrains – are at various stages of their development. Diesel has had the greatest influence on farms, with petrol and tractor vapourising oil (TVO) also featuring in the early development of farm tractors. The need for transition away from such fossil fuels has triggered the development of alternative, low emission fuels and is leading to the redesign of powertrains for tractors.
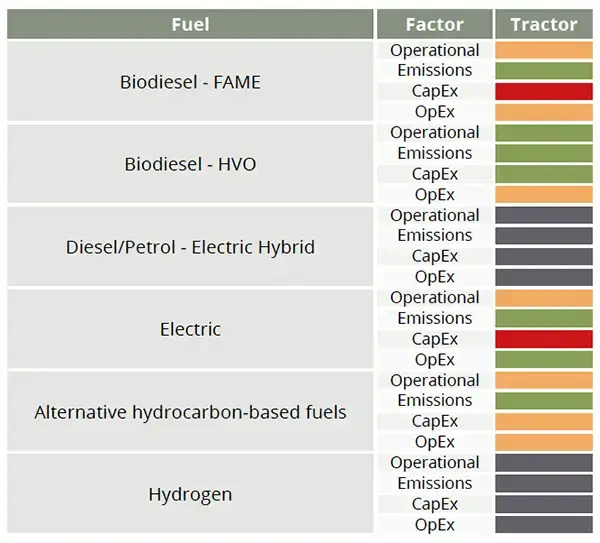
Traffic light assessment of potential fuel options. Source: Cenex
Farm vehicle design
The emergence of digitally controlled driverless (autonomous) technology and the need for more environmental and resource-sensitive field operations will lead to a revolution in vehicle design. With a move to low or no-till agriculture, lighter, smaller automated vehicles which are more suitable for electrification could become more widespread on farms and in horticultural enterprises.
The energy requirements of large farm vehicles make the use of battery electric technology unlikely in the near term as they would require huge and heavy batteries, regular high-power charging or battery swapping – all of which are impractical in a rural farm setting.
Farm vehicle transitions
It is unlikely that the UK farm sector will be able to go through multiple transitions from fossil-fuelled internal combustion engines (ICE), to FAME (fatty acid methyl esters, i.e. biodiesel derived from renewable sources), to biomethane and eventually to hydrogen used either in ICE or fuel cell systems.
More likely, due to long asset replacement cycles found on farms, only one or two transitions are likely before 2050. Coordinated planning of technology change, including by vehicle manufacturers, will help justify investment in selected technologies, help assure supply chains and drive down unit costs for farmers and growers.
Industry bodies and the UK government can provide leadership in this area. With the path to zero emission tailpipe vehicles still relatively unclear for non-road vehicles, biofuels and biomethane offer a short-to-medium term opportunity to reduce carbon emissions now. These ‘bridging fuels’ can provide significant CO2e savings in the short-term, while zero emission technologies improve, and battery and fuel cell prices fall.
Retrofitting farm vehicle engines
Given the long replacement cycle for farm vehicles and the fact that under 15,000 tractor units (including compacts) are sold each year in the UK, there should be greater scope for retrofitting cleaner, dedicated biomethane/bio-CNG engines.
This has already a proven technology as demonstrated by the JCB hydrogen ICE engine prototype planned to be installed in new JCB diesel backhoe loaders in 2023, also suited to retrofit.
ICE retrofit design and systems should be encouraged among engine manufacturers, not only as a means of keeping older (and perhaps vintage) units going.
On-farm renewable fuel generation
The RTFO (Renewable Transport Fuel Obligation) should encourage the shift to bio- and gas fuels in the next decade. Their operational similarities with fossil fuels will aid uptake as they require little change to adopt them. Renewable generation on-farm can improve the business case for battery powered tractors. It may also be possible, with dual-fuel or hydrogen ICEs plus development of better supply and refuelling infrastructure, to envisage a modest role for on-farm hydrogen over the same period.
Comparing renewable farm fuel options
A comparison of the potential alternative fuel options has been carried out for tractors as an example. Table 6 highlights the current situation. A red/amber/green (RAG) reporting system is used.
It is anticipated that in the next five years, HVO (hydrotreated vegetable oil or ‘renewable diesel’) and electric hybrids will become increasingly attractive as will alternative gaseous fuels such as CNG (compressed natural gas) and bio-CNG. It is expected that electric tractors will become more available and cost effective for lighter farm or horticulture duties.
The long term zero emission option of hydrogen is still many years away, the key challenge being access to an affordable and easily accessible supply of green hydrogen (via electrolysis) at a farm level to fuel initially ICE hydrogen engines and eventually fuel cell/electric hybrid tractors.
In choosing potential low carbon vehicles, farmers need to consider the following:
- The fuel
- Vehicle size and use patterns
- The capital and operating costs of the equipment
- The infrastructure requirements
This is a market that is rapidly changing. Table 7 provides an overview of the current technology options for tractors.
Technology maturity | Biodiesel (FAME / HVO) – Currently available. Diesel/Petrol - Electric hybrid – Not available. Electric – Small tractor (‘compact’) only. Alternative hydrocarbon-based fuel – Large tractor (agricultural) using CNG. Hydrogen – R&D prototypes only. |
Operational restrictions and benefits | Biodiesel FAME Increased maintenance regime; mineral diesel fuel and engine flush required before storage. Fuel quality requires monitoring and managing. Biodiesel HVO HVO is a ‘drop-in’ equivalent for diesel fuel. Alternative hydrocarbon-based fuel (e.g. biomethane) CNG/bio-CNG tractor requires a CNG/bio-CNG refuelling station, either on-site or within close driving range. Operating time is reduced significantly with on board CNG tanks. Ongoing development of LNG tanks on tractors will address this. Electric Reduced maintenance and operating costs resulting from the elimination of many service points compared to diesel machines. Operational time is limited (see below). Small ‘compact’ tractors only with c15 kW electric motor for small and light-duty work e.g. horticulture |
Operating time | Biodiesel The same operating time as diesel. Alternative hydrocarbon-based fuel (e.g. biomethane) Agricultural tractor example: CNG/bio-CNG tractor requires a CNG/bio-CNG refuelling station either on site or within close driving range. Electric Compact example: Farmtrac FT25G with electric indicative run time of 6 hours. |
Refuel / recharge time | Biodiesel Same refuelling time as diesel. Alternative hydrocarbon-based fuels (e.g. biomethane) Same refuelling time as diesel. Electric For example, the Farmtrac FT25G electric 240V has a 5-hour recharging time using a standard 32-amp outlet. |
Emission reduction | Biodiesel FAME Emission reduction variable depending on blend (circa 18% wheel-to-wheel WTW CO2 reduction available from B25 blend). Engine design, fuel quality and operational cycles essential in assessing total emissions with biodiesel – with some authors reporting in-creases in emitted NOx, particulates and CO. Biodiesel HVO (unblended) Circa 91% WTW115 CO2 reduction available. Alternative hydrocarbon-based fuels (e.g. biomethane) CO2 emissions reduced by 10% from CNG. Biomethane CO2 emissions depend on pro-duction route, but typically near zero. Very significant particulate matter (PM) and NOx reduction. Electric Zero at tailpipe, zero TTW116 emissions, WTW CO2 emissions depend on energy gener-ation, using grid rechanging the savings typically ~50-60% (based on DEFRA UK 2020 emission factors). |
Additional notes | Biodiesel – FAME Manufacturer approaches vary depending upon emission stage e.g. all John Deere engines can use biodiesel blends. Stage V engines operated within the European Union may use blends up to 8% (B8). Concentrations up to 20% (B20) can be used for all other John Deere engines providing that the biodiesel used in the fuel blend meets EU Standard (EN) 14214. Alternative hydrocarbon-based fuels (e.g. biomethane) Large (agricultural) tractor e.g. New Holland T6.180 Methane Power used to illustrate. It is the only biomethane option currently available in the UK (2022). Electric Smaller (compact) battery powered tractors e.g. FarmTrac FT25G electric provides an illustration. It is the only compact tractor option available currently in the UK (2022). |
Cost analysis | Diesel In the 2020 Budget, the UK government announced that it would be removing the entitle-ment to use red diesel from non-agricultural non-road mobile machinery (NRMM) in April 2022. No announcements have been made for the removal of subsidised ‘red’ diesel for agriculture. Biodiesel - FAME Plant Costs – For high biodiesel blend use, manufacturers may require a biodiesel upgrade package to be installed, typically costing several hundred pounds. For B100 use, the vehicles require a conversion to include a simple system for warming the fuel. Various conversions are available either at factory or retrofitted. These typically cost from £6,000 - £8,500 per vehicle. These are not likely to be available for small plant such as ATVs. Fuel Costs – Comparable to road diesel. Maintenance Costs – Some vehicle manufacturers suggest modified routines such as increased fuel filter and oil changes. Infrastructure Costs – Biodiesel blends up to B30 can be stored in and dispensed from existing infrastructure for diesel vehicles at no extra cost. B100 however needs to be kept at an appropriate temperature to ensure it remains liquid in the colder months. This will result in some heating costs. Bio-diesel - HVO Vehicle Costs – No impact on vehicle cost. Fuel Cost – Cost of fuel per litre is typically higher than road diesel. Maintenance Costs – Identical to those of diesel vehicles. Infrastructure Costs – No specialist equipment is needed to store HVO. Alternative hydrocarbon-based fuels (e.g. biomethane) Research suggests a 10% price premium for such systems. Fuel Costs – New Holland suggest a 30% reduction, but this is dependent upon CNG/bi-omethane prices. As a reference, a price quoted (Bennamann-Corserv) is £0.60 per kg. Electric Machine Costs – Research suggests a significant price premium. As an example, a FarmTrac FT25G fully electric costs are around 100% higher than its diesel equivalent. Fuel Costs – Estimated running cost for operators using an industrial electricity supply will be around 50% lower than for ‘red’ diesel and up to 60% lower than if using ‘white’ diesel. |
Biodiesel and biomethane market demands
Biofuels are limited in the amount of energy they can supply to the market. It has been suggested that biomethane can contribute 30% of the UK’s 2030 legally binding carbon targets. In the next decade, biofuels will be readily available for use in rural transport. This may not continue beyond 2030 as other market sectors seek to reduce their emission profiles.
However, the limited period of low competition for biofuels is not a justification for inaction in the agricultural sector. The move away from diesel use on farms needs to gain greater momentum and the industry must change but based on adaptation rather than revolution.
While UK food supplies cannot be put at risk, farmers need solutions for the next 20 years, including those based on the existing ICE engine technology.
There is a diminishing window of opportunity for cost-effective use of biofuels, due to the adoption of increasingly strict emissions legislation and increasing competition for biofuels across all market sectors. This has implications for low margin sectors like farming and hence there is a need to deploy farm produced biomethane as an early diesel replacement.
Also, there is a need to reassess the benefits of continued use of the internal combustion engine (ICE) on farms. Organisations that can make the financial and operational justifications for biofuels adoption today should do so as well as highlighting the wider potential of gas fuels.