by Dr Nick McCarthy
The transition to electric vehicles on farms has started, mainly on horticultural enterprises, for example electric compact tractors, quadbikes and small telehandlers are now available. On-road electric cars and vans are also growing in popularity. In the near future, driverless vehicles such as robots and gantries will be powered by electricity.
For this transition to succeed, accessible and reliable power supplies 24/7 – either from the grid or from on-farm renewables such as solar or wind – will be a co-requisite.
BEV charging infrastructure costs can be high and there are issues caused by the lower demand in dispersed rural areas and the weaker grid capacity often found in remoter areas. EVs can be charged either by using AC (grid) or DC (i.e. battery) electricity. There is good potential for on-farm DC microgrid systems to maximise on-site renewable electricity generation and battery storage for recharging farm vehicles and reduce the reliance upon grid electricity.
The table shows the primary capital outlay (assuming <5 metres of connection cable) for commercial BEV charge- points. The need for rural electricity grid reinforcement (to meet increased energy demand) can increase these costs significantly. Farmers and installers must address the options for grid reinforcement and cable lengths on a case-by-case basis.
AC or DC | Power | kW | Costs | |
---|---|---|---|
Standard | AC | 7-11 | £8,200 |
Fast | AC | 11-22 | £9,000 |
Rapid | AC | 43 | £11,000 |
DC | 50 | £30,000 | |
Ultra Rapid | DC | 150+ | 67,000 |
Biomethane
There has been significant investment in biomethane refuelling infrastructure by the likes of CNG fuels in recent years, but the sites are gas-grid connected and more suited to haulage fleets than farms. These central grid bio-CNG sites have a key role in haulage, but for farm use there is a need for virtual pipeline delivery or installation of biomethane upgrade plants on-site.
However, farm demand at a single location is unlikely to provide the year-round demand required to justify anything other than a smaller plant (perhaps 60 m3 to 150 m3 per hour output of bio-CNG). Biomethane uptake may therefore remain a niche option, unless installation of small biogas-to-biomethane upgraders on existing biogas sites can gain some traction. This will require some policy intervention, but on-farm biomethane does offer the only adoption-ready solution currently for the replacement of diesel. Demonstration sites are needed to expand this potential.
Small scale biomethane dispensing operations have been developed, based on the UK natural gas supply, with slow fill systems that can draw methane from natural gas infrastructure and store it on site (and can be adapted for on farm bio-CNG. There are examples in Europe where farm produced biomethane is being dispensed to service local community transport fuel needs.
Hydrogen
Hydrogen infrastructure faces similar barriers to biomethane. Renewable or ‘green’ hydrogen production is still undergoing technology development and if produced in quantity, dispensing prices may fall significantly in time. However, there is no guarantee that green hydrogen as a vehicle fuel will become price competitive with biomethane at a grid connected scale, let alone for smaller scale on-site modular systems.
Full replacement of diesel on farms with BEVs or hydrogen fuel cells may not be achievable or indeed appropriate before 2050. There are also issues with fuel cell durability in ‘dirty’ locations such as those found on farms.
Clearly, hydrogen or biomethane fuelled ICE engines can provide low margin industries such as farming with an affordable heavy power train. While some OEMs develop hydrogen engine technology, others are focused on biomethane as a pathway diesel replacement over the next 25 years.
However, investment decisions on hydrogen (for ICE) production, storage, and use should factor in the risk that future net zero legislation may not allow this option, but JCB and other ICE manufacturers plan to change this.
The use of hydrogen in adapted ICE’s could provide the demand for hydrogen as a fuel that would help facilitate adoption of cleaner hydrogen technologies such as fuel cells in the future. For low margin business sectors, operability issues (mud, dust, water, vibration) remain a concern for fuel cell ‘engines’, as are the high initial costs.
Replacing red diesel on farms
Emerging technology and fuel supply chain options will impact on future availability of clean fuels. Predicting technology innovation pathways needs vision, but it also tends to proceed in small leaps rather than large ones.
Clearly, the pace of change will be influenced by future adjustment of the red diesel subsidy. The NFU and other farmer representative organisations have raised concerns over the impact on farm profitability should the diesel subsidy be reduced or withdrawn – leaving farms paying the full price for diesel. However, there is a view that the industry’s low carbon credentials would be undermined if it is allowed to retain the subsidy beyond 2030.
Low-margin sectors such as farming cannot afford the inflationary impact of transport engine systems that rely on costly raw materials – often used in battery and fuel cell technologies. Farms need affordable, robust, high-torque power. Ahead of 2030, this can only be delivered at scale with biofuels (gas or liquid) using the internal combustion engine (ICE).
Biomethane offers the means to replace red diesel while facilitating the transition to other fuels like hydrogen. It is a farm and rural transport solution that can be cost comparable to diesel.
The pace of change depends on how cost-effectively fuel supply infrastructure and vehicle design change is implemented. JCB’s hydrogen ICE, based on a design initiated in 2020, will be on sale in the construction sector in 2023. The expected cost will not be inflationary because it uses adapted ICE technology and readily available materials and components.
Diesel replacement for farms and rural areas requires cost-effective power trains and better supply of green gas fuels (e.g. biomethane, ammonia, hydrogen). A government commitment is needed to show support for gas fuel generation systems and modified engines as a replacement for diesel and this will encourage more low and zero carbon emission ICE123 power trains to be developed.
Case study
JCB is investing in a zero-carbon future
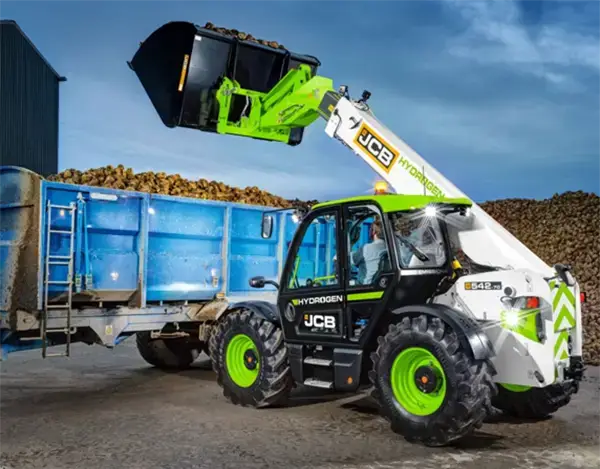
Replacement of diesel in farm and non-road vehicles is closer thanks to a revolutionary hydrogen fuel internal combustion engine (ICE) developed by construction machine manufacturer JCB.
The company has developed a combustion engine, using proven technology based on their conventional diesel ICE. It is fuelled by compressed hydrogen gas (H2), eliminating carbon emissions while keeping performance for non-road machines like its ubiquitous back-hoe loader.
Chairman of JCB, Lord Bamford, challenged JCB engineers to develop the hydrogen engine in 2020, He said at the launch in 2021, “My hope is that hydrogen power will be seen as a genuinely viable alternative to electric or battery-powered machinery within the construction sector. JCB is investing £100 million to produce super-efficient hydrogen engines.”
“JCB manufactures diesel engines. We are currently producing 400 a day for our own range of agricultural and construction machinery. However, with the Government’s commitment to end the use of diesel, we needed to look at alternative means of powering our machines.”
Development of the Hydrogen ICE Engineers developed the H2 ICE using established technology with readily available components.
The hydrogen back-hoe loader matches its diesel equivalent’s performance with an engine far less complicated than a hydrogen fuel-cell.
In July 2020, engineers at JCB Power Systems started designing the new engine. By December, the working prototype of a high-performance, zero-CO2 hydrogen fuel power train was being tested.
The four-cylinder (4.8-litre) H2 engine provides comparable power and torque to JCB’s ‘Dieselmax 448’ equivalent. Unlike battery powered (BEV) or fuel cell vehicles, the H2 ICE engine and the production vehicles will not be much more expensive than diesel versions, currently being trialled.
Lord Bamford commented, “It is robust, cost-effective and it could be integrated into all forms of powertrain. Most importantly, a familiar technology and lack of complexity make hydrogen an ideal zero carbon solution for our customers and our supply chain.”
JCB is developing a telehandler for on farm and other uses, more powerful than its current electric offering.
Hydrogen ICE – a Propulsion System for the Future
JCB machines often operate well away from existing infrastructure – on farmland, in quarries or on construction sites. BEVs are impractical for equipment with high power demand in such locations.
For such heavy-duty vehicles, batteries would weigh too much and cost too much. There would be insufficient time to charge them, even if on-site charging infrastructure was in place. With its cost comparable to a traditional engine, unlike battery power, the ICE is not inflationary.
JCB expect the first H2 ICE machines to be supplied to customers in 2023. Widespread adoption requires access to green hydrogen supply from surplus renewable energy generated by solar or wind power. Lord Bamford hopes that green hydrogen power will be a key part of the solution to climate change.